
The Facts About Building with Treated, Engineered Lumber

"The word ‘treated’ can mean wildly different things."
Outdoor living is big in the Pacific Northwest, and because of that we sell a lot of materials for decking projects of all sizes. For some second story decks, property owners are asking for fewer vertical posts in order to maximize their view and create a cleaner looking structure. These requests have led to more calls for treated, engineered wood beams that handle these larger spans. This article was created to look deeper into this topic.
Perception versus reality
When most people hear the word “treated” in conjunction with building materials, they think the product will be protected from rot and decay. Some might even assume there's a warranty that supports that impression.
Unfortunately, when it comes to most treated, engineered lumber products, neither of these assumptions are true.
Process challenges
So what is standing in the way of the seemingly simple request for fewer vertical deck posts? Well, there are a few things:
- The companies that typically treat engineered lumber products are not the same companies that manufacture the products. For that reason, the manufacturers will oftentimes state that any warranty that comes with their products is null and void if the products are exposed to some form of treating process.
- The treating companies trying to extend the life of these engineered products face other hurdles when trying to provide a warranty. Engineered lumber frequently has a protective coating or layer of some kind (wax, etc.) that makes it difficult for the treatment to adequately penetrate the product. Without the proper penetration, there can be no warranty against rot and decay.
- And, many times (at least in the Western U.S.) engineered lumber products will be made from a significant amount of Douglas fir and larch wood fiber. These species are oftentimes only treated to a “point of refusal” and don't consistently meet the necessary chemical penetration to support a warranty for rot and decay.
It’s still treated, right? What’s the big deal?
When it comes to the different processes out there, the word “treated” can mean wildly different things. One popular treatment marketed to protect against rot and decay for engineered wood products is really more of a heavy-duty insect repellent than a preservative. But contractors and homeowners are at risk when they assume a higher level of protection than is real. Think of this scenario: A second level deck is built using a treated, engineered lumber beam to minimize the number of required vertical supports.
First off, maybe the treatment isn’t as good as presumed.
Then the ends of the beams are trimmed to fit the length, leaving those cut ends exposed.
Then the beams are placed inside a post-to-beam bracket or connector of some kind, trapping moisture in the bracket.
Then structural fasteners are used to connect the beam to the post-to-beam bracket, adding additional penetrations at the beam ends.
Without proper treatment of end cuts and penetrations and a well-designed cap flashing for the top of the beam that will keep water from collecting inside the post-to-beam bracket, you have a recipe for disaster.
Best practices for the job site
If you're concerned after reading this, I understand. That was a large part of our motivation for writing this article—to help create awareness. So what are your options?
- If possible, use solid sawn, pressure-treated lumber where you know the warranty for rot and decay stays intact when installed properly (treating end cuts and penetrations, etc.). This may involve adding additional support posts, which may or may not be a deal-breaker for the property owner.
- If using treated, engineered lumber, install it (protect it) like it was a non-treated, softwood lumber species. That means think like a drop of water: If the material is continually exposed to moisture, you're at risk for challenges in the future. Treat cut ends and use appropriate flashing profiles to keep water away from the material. Evaluate the build structure and identify areas where water or moisture could accumulate and compromise your building materials.
- If using adhesive-backed flashing tape, only use butyl products. Do not use asphalt products.
- Although currently pretty rare, there are a handful of engineered lumber products manufactured with warranties against rot and decay. Weyerhaeuser’s Parallam Plus PSL is one of them. They use primarily Southern Yellow Pine that is much more suitable for treating. Unfortunately, these are harder to find in the Western U.S due to high shipping costs.
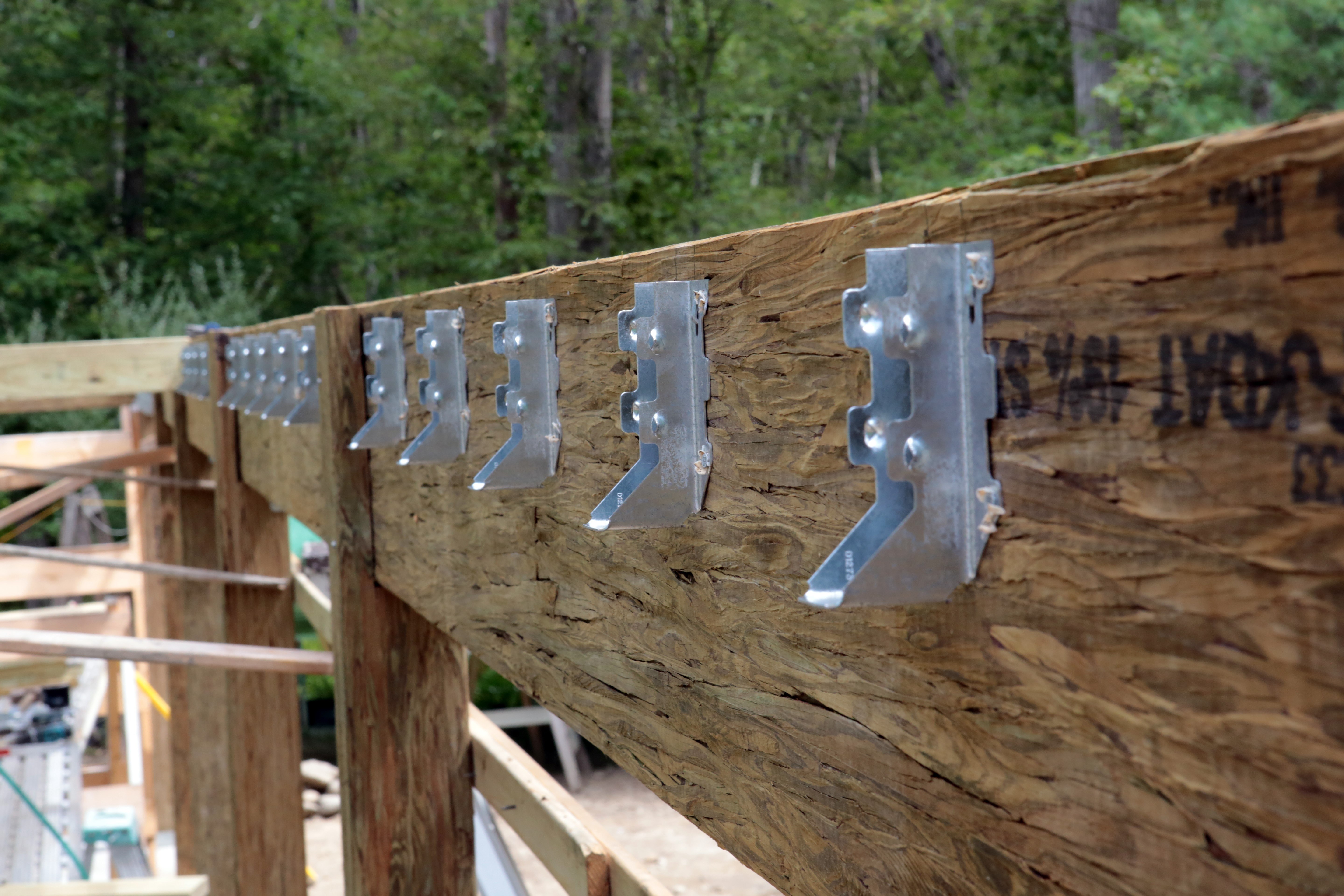
In summary, there will continue to be deck design specifications requiring an engineered lumber solution. If and when you encounter this, know the limitations of the products you're building with and protect them accordingly. We're hopeful that more and better options are coming in the future, and we're committed to keeping you updated on this subject.